Digital transformation has emerged as the key for manufacturers to meet rising demands, achieve sustainability goals, and increase efficiency. As a result despite this, 45% of manufacturers plan to adopt smart technologies within the next year and avoid falling behind competitors.
In this report, discover the top 10 digital transformation technologies driving the manufacturing industry. This article also provides a step-by-step guide to digitizing your operations to enhance operational efficiency, reduce costs, and improve product quality.
Key Takeaways
- The Time to Act Is Now: Manufacturing is under pressure from economic challenges, performance demands, and shifting customer expectations.
- Top 10 Digital Transformation Technologies in the Manufacturing Industry
- Key Benefits: Digital transformation enhances quality, increases process efficiency, and increases profit margins.
- Step-by-Step Guide: With only 42% of leaders adopting digital transformation, manufacturers need to define goals, assess readiness, and implement high-impact technologies.
- Future Trends: Decentralized production, immersive technologies, and advanced workforce training drive supply chain resilience and enhance collaboration.
How do we research and where is this data from?
We reviewed over 3100 industry innovation reports to extract key insights and construct the comprehensive Technology Matrix. To increase accuracy, we cross-validated this information with external industry sources.
Additionally, we leveraged the StartUs Insights Discovery Platform – an AI and Big Data-powered innovation intelligence tool covering over 4.7 million startups and more than 20K+ technologies & trends worldwide to:
- Confirm our findings using the Trend Intelligence feature.
- Gather market statistics for each technology.
- Identify startups for the “Spotlighting an Innovator” sections.
Why the Time to Act is Now
Rising Economic Pressure
The rising global competition in manufacturing is accelerating the adoption of digital transformation. 89% of manufacturers have adopted or are planning to adopt a digital-first strategy.
As per McKinsey’s report, digital transformation boosts throughput by 10-30%, reduces machine downtime by 30-50%, and improves labor productivity by 15-30%.
Source: McKinsey & Company
Investment in digital transformation is soaring, with the global market projected to reach USD 110.1 billion by 2028, at a CAGR of 61.3%. Additionally, 58% of companies intend to increase spending on digital initiatives.
Source: Research and Markets
Changing Customer Expectation
Customers demand high-quality, personalized products to be delivered quickly. This is a significant catalyst for digital transformation in manufacturing.
88% of companies have prioritized sustainability due to increasing consumer demand for eco-friendly practices. Manufacturers also indicated that AI and machine learning have the largest impact on business outcomes relative to other smart manufacturing technologies.
Top 10 Digital Transformation Technologies in the Manufacturing Industry (2025)
1. 3D Printing or Additive Manufacturing
Additive manufacturing enables lighter components without compromising strength, eliminates the need for tooling and molds, and reduces inventory costs. These benefits lead to faster time to market, improved product quality, and increased manufacturing efficiency.
As per KBV research, the global 3D printing market size is expected to reach USD 86.4 billion by 2030, rising at a market growth of 21.4% CAGR during the forecast period.
The growing demand for prototyping applications across various industries and verticals, combined with aggressive research and development in additive manufacturing, is expected to drive market growth.
Source: Grand View Research
Taking a deeper look into regions globally, North America accounted for the largest share of the 3D printing market share i.e. 38.1% in 2023.
Source: MarketsandMarkets
One of the promising developments of the 3D printing market industry is the introduction of the F3300 fused deposition modeling (FDM) 3D printer by Stratasys.
Market Insights & Growth Metrics
Scale and Magnitude
According to StartUs Insights, 3D Printing has seen substantial growth, with 17 360+ companies operating globally. This is reflected in the growing market from USD 23.41 billion in 2025 to USD 101. 74 billion exhibiting a CAGR of 23.4%.
It holds a decent media presence, ranking 156th among emerging technologies, reflecting a fair level of public and media attention. In the automotive sector, which leads in 3D printing adoption, the market is expected to reach USD 16 billion by 2034, growing at a CAGR of 19.40% from 2024 to 2034.
Source: Towards Automotive
Similarly, the aerospace industry has seen notable advancements, with its 3D printing market projected to grow at a CAGR of 20.6%.
Growth Indicators
According to our data, interest in 3D printing continues to grow with a 42.84% annual increase in search interest. Funding in additive manufacturing has also risen significantly, showing a 67.54% growth over the past five years.
The top 100 funded 3D printing startups raised amounts ranging from USD 200 000 to USD 50 million in various funding rounds throughout 2024.
Innovation and Novelty
Based on our database, the 3D printing sector stands out as a center of innovation, demonstrated by over 179 470 patents filed worldwide. Patent filings in 3D printing grew eight times faster than the average of all technologies in the last decade. Moreover, 3D printing research has been supported by only 4625 grants.
Top Use Cases of 3D Printing in Manufacturing
- Prototyping and Product Development: Rapid creation of physical models facilitates swift iterations and improves form, fit, and function testing.
- Tooling and Fixtures: 3D printing enables custom tools, jigs, and fixtures by enabling intricate geometries. They reduce cycle times and increase cost-efficiency.
- Lightweight Structures: By utilizing lattice structures and optimizing material distribution, manufacturers reduce weight. This design flexibility improves performance and fuel efficiency.
- Casting Patterns and Molds: 3D-printed molds produce complex metal parts with high accuracy. This reduces lead times and costs associated with traditional mold-making.
Noteworthy 3D Printing Advancements
- Relativity Space’s Stargate: It has secured a USD 8.7 million contract with the U.S. Air Force Research Laboratory to develop real-time flaw detection in large-scale 3D printing. This initiative aligns with congressional directives to leverage additive manufacturing for accelerating aerospace component production.
- Triditive’s AMCELL Printers: The Amcell 8300 is designed for mass production, featuring eight customizable robots and a build volume of 300 mm in diameter by 350 mm in height. The Amcell 1400 caters to large-scale part manufacturing with a build volume of 450 x 400 x 500 mm and supports polymers, composites, and metals.
Core Technologies to 3D Printing
- Fused Deposition Modeling (FDM): Creates durable, functional prototypes and end-use parts by layering thermoplastic materials. For example, automotive companies use it to quickly produce robust prototypes for testing vehicle interiors.
- Stereolithography (SLA): Uses UV lasers to solidify liquid resin into highly detailed parts. It is ideal for precision applications like dental molds or complex jewelry designs.
- Selective Laser Sintering (SLS): Fuses powdered materials with a laser to create complex geometries and high-strength parts. Aerospace companies use SLS to manufacture lightweight, durable components for aircraft.
Spotlighting an Innovator: Desktop Metal
Desktop Metal, based in the US, specializes in metal, polymer, and ceramic part 3D printing technologies for applications in aerospace, automotive, and medical devices.
The company announced a USD 183 million merger agreement with Nano Dimension. Recent highlights include launching the PureSinter Furnace, expanding its material portfolio to over 40 options, and showcasing aluminum 3D printing advancements.
Desktop Metal also partnered with Eaton to innovate in binder jet 3D printing.
2. Industrial Internet of Things
IIoT is enabling smarter, data-driven operations through connected devices and systems. It optimizes efficiency, reduces downtime, and improves decision-making.
The IoT in manufacturing market size is projected to reach USD 1495 billion by 2030, growing at a CAGR of 22.6% from 2025 to 2030. In the US, the IIoT market size is expected to grow at a CAGR of 18.6% from 2024 to 2030.
Source: Allied Market Research
A key driving factor for IoT adoption in manufacturing is the demand for real-time asset monitoring. The growing need to predict equipment failures and minimize unplanned downtime significantly propels its growth.
The growing adoption of connected devices is reflected in the increasing number of IIoT connections – anticipated to reach USD 13.8 billion by the end of 2025.
McKinsey estimates the economic impact of IoT (including IIoT) to reach USD 11 trillion by 2025, underscoring its vast potential across industries
By 2025, the IIoT market value is expected to reach USD 500 billion, fueled by advancements in technologies like 5G, AI, and edge computing.
Market Insights & Growth Metrics for Internet of Things
Scale and Magnitude
Based on our data, there are over 22 345 companies globally operating in the IIoT sector. They provide innovative solutions across industries like manufacturing, aerospace, and automotive. By 2025, the broader industrial IoT market is expected to reach USD 593.8 billion, driven by advancements in technologies like AI, edge computing, and digital twins.
IIoT holds the 301st position in media coverage among emerging technologies in our database. Though it might not receive the same level of public attention as consumer-facing technologies like AI or blockchain, IIoT is making an impactful entry within industrial domains. As of February 12, 2024, the Industry IoT Consortium (IIC) reported having 224 member organizations, reflecting the expanding interest and participation in IIoT initiatives.
Growth Indicators
StartUs Insights’s most recent data suggests that IIoT has experienced a 54.61% annual increase in search interest. This growth highlights the expanding relevance of IIoT in various applications, from smart homes to industrial automation.
In 2024, the top 20 IoT startups collectively received nearly USD 6.7 billion in funding which accounts for 31% of all investments.
Source: IoT Business News
Despite the rise in interest, IIoT’s five-year funding growth has declined by 54.51% according to our database. This trend may stem from market saturation in specific IIoT segments, as established players dominate certain niches.
Innovation and Novelty
The IIoT sector has seen significant innovation, with over 96 445 patents filed globally based on our data. Leading companies in IoT patent holdings include Samsung Electronics, LG, and Qualcomm.
Moreover, StartUs Insights reports that IIoT-focused research has received 1770+ grants. The U.S. led in IoT patent filings for the retail industry with a 57% share in Q3 2024, followed by China (5%) and Australia (2%). NIKE filed the most IoT patents in the retail industry in Q3 2024 with 18 applications.
Source: Power Technology
Top Use Cases of Industrial Internet of Things in Manufacturing
- Remote Monitoring: IIoT enables real-time tracking of equipment and production processes to reduce manual inspections and enable rapid anomaly response.
- Predictive Maintenance: By analyzing sensor data and identifying patterns from the data collected from IIoT systems, such solutions predict equipment failures to minimize unplanned downtime and extend machinery lifespan.
- Inventory Management: IIoT facilitates automated tracking of inventory levels using connected systems to optimize stock levels and prevent shortages or overstocking. This ensures smooth supply chain operations.
- Asset Tracking: IIoT solutions track the location and condition of assets in real-time to improve visibility into the movement and usage of tools, machinery, and raw materials.
Noteworthy IoT Advancements
- Knowix’s Partnership with Applied Fiber: They collaborated to introduce a digital IIoT termination solution for high-performance cable and rope systems. It integrates Applied Fiber’s socketed terminations with Knowix’s sensor and data technology.
- Softeq’s IIoT Solutions: The company adds smart capabilities to analog equipment. This automates manufacturing processes and increases production levels. Their services encompass predictive maintenance, AR remote assistance, and more.
Core Technologies Connected to the Internet of Things
- Smart Sensors: Collect and transmit data on various parameters, such as temperature, humidity, and vibration, to deliver real-time insights into industrial processes.
- Connectivity Protocols: Standards like MQTT, OPC-UA, and industrial-grade Wi-Fi ensure secure and reliable communication between IIoT devices and systems.
- Cloud Computing: Provides scalable storage and processing power to aggregate and analyze vast amounts of data generated by IIoT devices for actionable insights.
Spotlighting an Innovator: Memfault
Memfault, a US-based company, develops an IoT reliability platform that provides embedded observability tools. The platform collects diagnostic data directly from devices deployed in the field. It aggregates and analyses the data in the cloud to identify, monitor, and resolve issues such as crashes, performance bottlenecks, and firmware bugs.
Integrating automated crash reporting, over-the-air firmware updates, and fleet performance monitoring further allows developers to manage millions of devices efficiently.
Memfault recently launched “Product Analytics,” offering deep insights into IoT device performance and user behavior.
3. Augmented Reality and Virtual Reality
AR and VR enable immersive, data-driven operations through advanced visualization and simulation technologies. These technologies reduce downtime and improve decision-making.
As per Precedence Research, the global AR and VR manufacturing market size is projected to reach USD 74.1 billion, growing at a CAGR of 24.62%.
Source: Precedence Research
Several factors are contributing to the growth of AR and VR in the manufacturing industry and one of the key reasons is designing the manufacturing site with emerging technologies.
Augmented reality improves worker safety and productivity. Therefore, many developing nations are taking initiatives and setting industry standards to drive the adoption of AR and VR on a global scale.
Significant investments from major players like Microsoft, Google, and Samsung are driving innovation, with adoption rates highest in North America and rapid growth anticipated in Asia Pacific to grow at the highest CAGR of over 41% from 2025 to 2030.
Notably, partnerships like the ESI Group and CIMPA collaboration exemplify how AR/VR integration with lifecycle management is shaping the future.
Augmented reality is favored for its ability to enhance training, process efficiency, and employee well-being, while VR, with its immersive 360-degree capabilities, is set to grow at 32% CAGR, fueled by trends like smart factories and industrial IoT.
Source: Finances Online
Market Insights & Growth Metrics for Augmented and Virtual Reality
Scale and Magnitude
According to StartUs Insights, Augmented Reality has seen substantial growth, with 22 410+ companies operating globally. The global augmented reality and virtual reality market involves numerous players including major tech companies like Google, Sony, Apple, Samsung, and others.
According to StartUs Insights, a media presence rank of 159 for Augmented Reality (AR) indicates moderate visibility. AR garners significant attention, particularly in niche sectors like manufacturing and gaming.
In 2024, the most important use cases for AR/VR were VR gaming, VR video/feature viewing, and VR gaming, with a market volume of USD 17.6 billion.
Source: Art Labs
Growth Indicators
Interest in Augmented reality continues to grow, with a 17.68% annual increase in search interest whereas the interest in virtual reality grows with 19.72% in search interest. The use of AR in retail is projected to be worth USD 62.3 billion by 2033, with a CAGR of 41.7%
As per our data, funding in AR funding has surged 88.10% over five years, while VR funding declined 9.75%.
This momentum is evident through investments like ArborXR’s USD 12 million Series A for enterprise AR/VR management and VividQ’s USD 7.5 million to advance holographic display technology.
In Europe, AR/VR spending is projected to grow at a 21.9% CAGR over the next five years reaching USD 10.2 billion by 2028.
Source: IDC
Innovation and Novelty
According to our data, the existence of 68 280 AR patents and 131 759 VR patents underscores significant innovation and investment in immersive technologies, signaling a robust market interest in both.
Between 2022 and 2024, the highest number of AR technology patent applications were filed in 2022 with 26 patents, and in 2024, the grants were reduced to 7 patents.
The substantial patent activity highlights the growing competition and opportunities for market players to develop unique solutions and capture emerging demands in these rapidly evolving sectors.
Top Use Cases of AR and VR in Manufacturing
- Training and Skill Development: AR/VR provides immersive, hands-on training environments to enhance workforce knowledge retention and reduce training time compared to traditional methods.
- Assembly Guidance: AR overlays real-time, step-by-step instructions onto physical components, assisting workers during complex assembly tasks and improving accuracy.
- Design and Prototyping: VR enables engineers to create and iterate on digital prototypes rapidly without waiting for physical models, accelerating design cycles and facilitating human-centered design by simulating user interactions with products.
- Remote Collaboration: AR/VR facilitates remote collaboration among teams, allowing engineers from different locations to work on the same 3D models, improving product development efficiency and reducing travel expenses.
Noteworthy Augmented and Virtual Reality Advancements
- VividQ’s Collaboration with Dispelix: They developed a ‘waveguide combiner’ to accurately display simultaneous variable-depth 3D content within a user’s environment. This enables immersive augmented reality gaming experiences.
- DHL’s Vision Picking: This initiative employs smart glasses equipped with augmented reality to guide warehouse staff through picking processes. In a pilot project conducted in the Netherlands, this technology led to a 25% increase in efficiency during the picking process.
Core Technologies Connected to Augmented and Virtual Reality
- Smart Glasses and Headsets: Overlay step-by-step guidance directly onto physical components during assembly, reduce errors, and improve efficiency. It also aids in hands-free operations that allow workers to stay focused on tasks while accessing critical information.
- 3D Modeling and Simulation Software: Supports the design and prototyping process by enabling engineers to test and refine concepts in virtual environments. In operations, 3D simulation helps in planning and optimizing workflows and ensures seamless integration of new processes or equipment.
- Spatial Computing: Combines AR, VR, and AI to map and interact with physical spaces in a digitally enhanced manner. In manufacturing, this technology enables precise spatial mapping of facilities, allowing for optimized layouts, equipment placement, and safety planning.
Spotlighting an Innovator: Autovrse
AutoVRse, based in India, provides AI-powered VR and AR solutions for immersive enterprise training across industries like manufacturing, automotive, and oil and gas. Its VRse Builder platform has trained over 300 000 workers and served 100+ enterprises, including Shell, Bosch, and Tata Motors.
The company recently raised USD 2 million in seed funding led by Lumikai, partnered with JSW to train 50 000 employees in workplace safety by 2025, and announced the launch of “District M,” a VR rhythm game.
4. Robotics
Robotics in manufacturing fills workforce gaps to improve safety and boost productivity through the automation of repetitive and hazardous tasks.
As per Precedence Research, the global robotics technology market is estimated to reach USD 372.59 billion by 2034, growing at a CAGR of 14.70% from 2024 to 2034.
Source: Precedence Research
Advancements and innovations in the robotics industry are key drivers of its growth, enabling transformative applications across sectors. Mobile manipulators (MoMas), for instance, combine mobility with manipulation capabilities, allowing them to perform diverse tasks such as inspections and maintenance work.
Additionally, collaborative robots (cobots) are revolutionizing the industry, now accounting for 10% of new robot installations and growing faster than traditional robots.
These innovations not only enhance operational efficiency but also reduce costs by up to 30%, minimize human error, and improve product quality, solidifying robotics as a cornerstone of modern manufacturing.
Market Insights & Growth Metrics for Robotics
Scale and Magnitude
Based on our data, there are over 75 042 companies globally operating in the Robotics sector. They provide innovative solutions across industries like manufacturing, healthcare, agriculture, logistics, food, and pharmaceuticals.
In the first 12 weeks of 2024, robotics startups secured USD 748.9 million in funding with March alone accounting for USD 642 million across 37 firms.
Robotics holds the 30th position in media coverage among emerging technologies in our database. This indicates moderate attention compared to other tech domains.
Growth Indicators
StartUs Insights reports that Robotics has experienced a 3.85% annual increase in search interest. The global operational stock of industrial robots reached 4 281 585 units, marking a 10% increase from the previous year.
Source: IFR
Robotics’ five-year funding growth has increased by 24.57%, according to our database. Moreover, robotics startups collectively raised over USD 4.2 billion in funding in 2024.
Increasing demand for automation across multiple sectors is driven by labor shortages increasing competitiveness and a shift from mass production to mass customization.
Innovation and Novelty
The Robotics sector has seen significant innovation, with over 424 465 patents filed globally based on our data.
The World Intellectual Property Organization (WIPO) reports that AI patent families, which often overlap with robotics, increased from 733 to more than 14 000 between 2014 and 2023, representing an over 800% increase.
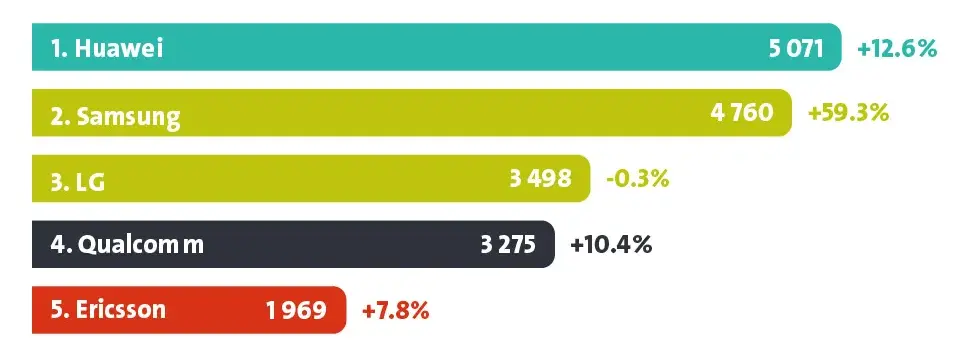
Source: EPO
Leading companies in robotics are Hyundai Motor, VW Group, Samsung, LG, iRobot, and others. StartUs Insights reports that Robotics-focused research has received 11 223 grants.
Top Use Cases of Robotics in Manufacturing
- Assembly Automation: Robotic arms equipped with advanced sensors and actuators handle intricate assembly tasks, such as fitting small components and fastening parts, with minimal error.
- Material Handling: Advanced robotic manipulators equipped with machine vision systems identify, pick, and place items with precision. This capability significantly reduces manual effort, especially in large-scale operations with critical speed and accuracy.
- Robotic Welding Systems: These systems leverage machine vision and advanced control algorithms to perform arc welding, spot welding, and laser welding. The integration of sensors ensures consistent weld quality while minimizing material wastage.
- Quality Inspection: Uses machine vision and AI-powered algorithms to detect real-time defects. Robots with high-resolution cameras and precision actuators inspect products for dimensional accuracy, surface flaws, and structural integrity.
Noteworthy Robotics Advancements
- Bear Robotics’ Launch of Nex-Gen Autonomous Navigation: The company secured a USD 60 million Series C funding exclusively led by LG Electronics. This strategic investment propels Bear Robotics into emerging markets such as smart warehousing and supply chain automation.
- Spot Robot Enhances BMW’s Maintenance Data Collection: BMW’s Hams Hall plant has integrated Boston Dynamics’ Spot robot to enhance data collection for its digital twin. Equipped with IoT sensors, Spot autonomously gathers temperature readings, and manual dial measurements, and detects acoustic anomalies.
Core Technologies Connected to the Robotics
- Cloud Robotics: Integrates robotic systems with cloud-based resources for robots to share information, learn collaboratively, and optimize operations in real-time.
- Machine Vision and Computer Vision: Enable robots to see and interpret visual data for decision-making. Machine vision aids in object recognition, defect detection, and assembly verification.
- Sensors and Actuators: Proximity detectors, force sensors, and temperature sensors gather critical data, while actuators translate this data into precise movements. These components allow robots to perform material handling, assembly, and more.
Spotlighting an Innovator: Robust AI
Robust.AI, based in the US, develops collaborative mobile robots for warehouses and manufacturing, with its flagship product, Carter, designed to work alongside humans using AI-driven awareness and adaptive responsiveness.
The company recently launched Carter Pro, featuring enhanced AI capabilities and improved human-robot interaction for industrial efficiency.
Robust.AI emphasizes supporting human workers rather than replacing them. The company has secured funding to advance its technology and continues to focus on scalable, collaborative productivity in industrial settings.
5. Digital Twins
Digital twins enable real-time monitoring, simulation, and optimization of manufacturing operations. It reduces downtime and improves decision-making abilities.
The implementation of digital twins in manufacturing has shown significant benefits, including up to 40% reduction in maintenance costs and up to 15% increase in overall equipment effectiveness (OEE).
Source: Hexagon
According to Fortune Business Insights, the global market for digital twins is set to increase from about 16.42 billion in 2024 to 240.11 billion by 2032 with an annual growth rate of 39.8%.
Source: Fortune Business Insights
The adoption rate of digital twins in manufacturing is expected to grow tenfold.
For example, the Asia Pacific region is expected to experience substantial growth in the digital twin market, with a projected CAGR of 36.7% from 2024 to 2030.
This technology accelerates project creation and setup, reducing the time to launch AI-enabled features by up to 60% and lowering costs by approximately 15%.
Market Insights & Growth Metrics for Digital Twin
Scale and Magnitude
According to StartUs Insights, the digital twin sector comprises over 5995 companies globally, with the US market projected to grow from USD 7.3 billion in 2024 to USD 104.8 billion by 2033 at a CAGR of 34.5%.
Despite ranking 689th in media coverage among all emerging technologies, digital twins continue to gain traction, with Siemens leading as a frontrunner in the field.
Growth Indicators
StartUs Insights reports there has been a 26.72% annual increase in search interest for digital twins. This reflects growing curiosity and adoption across various sectors.
Approximately 70% of technology leaders in major corporations actively pursue and allocate resources to digital twin initiatives
The digital twin market has seen substantial growth in recent years, with projections showing an increase from USD 17.73 billion in 2024 to USD 259.32 billion by 2032.
Increasing public and private investments in digital transformation solutions are also creating robust opportunities for market growth.
Innovation and Novelty
StartUs Insights reports that the digital twin domain has witnessed substantial innovation with over 6308 patents filed globally. IBM and Siemens are the top digital twin patent filers.
China leads in digital twin patent filings with 5217 patent families, followed by the USA with 825, and the European Union with 545.
Source: Harrity
Top Use Cases of Digital Twin in Manufacturing
- Factory Design and Layout Optimization: Digital twins enable manufacturers to simulate and test factory layouts virtually. It optimizes space utilization, improves workflow efficiency, and identifies bottlenecks.
- Schedule Optimization: By simulating production scenarios and dynamically adjusting schedules based on real-time data, digital twins streamline resource allocation and minimize downtime.
- Predictive Maintenance: Digital twins leverage real-time IoT sensor data to predict equipment failures and schedule proactive maintenance. This reduces unplanned downtime and maintenance costs significantly.
- Quality Control: Through virtual simulations and real-time sensor data analysis, digital twins identify potential quality issues early, reduce reliance on physical prototypes, and ensure consistent product standards.
Noteworthy Digital Twin Advancements
- Unilever’s Virtual Factory Replicas: Its Dubai Personal Care (DPC) factory simulates and analyzes operations to optimize production and predict potential equipment breakdowns. This minimizes downtime and extends equipment lifespan.
- Siemens’ Collaboration with KU Leuven: This initiative aims to advance digital twin technologies focusing on applications in industrial electromechanical systems, machinery, drives, and transportation vehicles. The collaboration seeks to address societal, industrial, and technological challenges through interdisciplinary efforts and partnerships.
Core Technologies Connected to Digital Twin
- Internet of Things: Forms the backbone of digital twins by continuously collecting real-time data through sensors and feeding it into digital twin models. This enables seamless monitoring and connectivity for dynamic production line adjustments.
- AI and ML: Enhance digital twins by forecasting equipment failures using predictive analytics and analyzing historical data to identify patterns.
- 3D Modeling and Simulation Software: Advanced software like Autodesk Fusion and FlexSim facilitates the creation of dynamic digital twins by enabling rapid prototyping, virtual testing of performance, and accurate system behavior representation.
Spotlighting an Innovator: Tomorrow Things
Tomorrow Things, a German startup, develops an intelligent automation platform for creating digital twins of technical assets. This enables real-time monitoring, optimization, and seamless ecosystem integration for industries like manufacturing.
The company recently raised EUR 1.5 million in funding from investors such as HTGF and neoteq ventures to enhance its AI-powered Operating System for machines.
6. Edge Computing
Edge computing processes and stores data near the origin of the data. It minimizes the time consumed for gathering, processing, and analyzing large volumes of unstructured data.
The edge computing market research was valued at USD 38.2 billion in 2024 and is expected to grow at a CAGR of 44.7% reaching USD 1065.63 billion by 2033.
Source: Straits Research
The European market is anticipated to witness significant growth, with a CAGR of around 35% from 2024 to 2030. The surge in edge computing adoption has attracted substantial investments from major technology companies and venture capitalists.
Leading firms in this domain are Amazon Web Services (AWS), Cisco Systems, General Electric, and Hewlett Packard Enterprise (HPE).
Additionally, enterprises across various industries have demonstrated increasing interest in edge computing, with its adoption gaining momentum in recent years. For example, Dropbox has implemented an edge network to enhance connectivity and expedite user access
Market Insights & Growth Metrics for Edge Computing.
Scale and Magnitude
Edge Computing technology has grown significantly with 46 000+ companies currently operating in the domain based on our data.
This growth aligns with US market projections, which are anticipated to reach USD 7.2 billion in 2025, growing at a CAGR of 23.7% from 2025-2033.
The manufacturing sector had the highest adoption rate for edge computing at 8.4%, nearly three times higher than the next leading industry sector.
StartUs Insights reports that edge computing ranks 226th in media coverage among 20K+ emerging technologies despite its broad applications. This reflects moderate attention compared to other technologies like AI and cybersecurity.
Growth Indicators
Our analysis highlights the remarkable growth of edge computing, evidenced by an 89.95% annual rise in search interest and a 197.08% increase in funding based on our data.
By 2028, global edge computing spending is expected to approach USD 378 billion.
Source: IDC
North America is expected to dominate the edge computing market throughout the forecast period – capturing more than 40% of the worldwide total share.
Innovation and Novelty
As per our data, edge computing remains a highly innovative domain with 20 478+ patents filed globally. Moreover, edge computing-related research is also supported by 5670+ grants, showcasing institutional and governmental support.
In 2015, there were only 720 new papers related to edge computing on Google Scholar. By 2023, this number had grown to more than 42 700, indicating substantial academic and institutional focus on advancing this technology.
Top Use Cases of Edge Computing in Manufacturing
- Predictive Maintenance: By processing data from IoT sensors at the network’s edge, edge computing enables real-time monitoring of equipment health. It facilitates immediate anomaly detection and predictive maintenance strategies.
- Video Surveillance: Edge computing allows for the local analysis of video feeds for real-time detection of security breaches or quality control issues without the latency associated with cloud processing.
- Condition-based Monitoring: Edge computing processes sensor data locally to monitor machinery conditions in real time. This enables immediate responses to deviations and supports condition-based maintenance approaches.
- Data Management: Edge computing reduces the volume of data transmitted to central servers by processing and filtering information locally to enhance data management efficiency and ensure timely decision-making.
Noteworthy Edge Computing Advancements
- Rockwell Automation’s Partnership with ZEDEDA: By integrating ZEDEDA’s edge orchestration solution, Rockwell Automation enables manufacturers to manage edge devices, orchestrate applications, and improve access to manufacturing data.
- ABB’s Collaboration with Red Hat: By utilizing Red Hat OpenShift and Red Hat Device Edge, ABB extends applications to the industrial edge. This enables low-latency data extraction from control systems while improving device onboarding and policy management.
Core Technologies Connected to Edge Computing
- 5G Connectivity: Enables ultra-low latency and high-bandwidth data transmission. It facilitates real-time processing and decision-making for advanced manufacturing applications.
- AI and ML: Allow for immediate analysis and interpretation of data generated by manufacturing equipment. It supports functions such as predictive maintenance, quality control, and process optimization without centralized cloud resources.
- Distributed Computing Architecture: Processes data closer to its source to reduce latency and bandwidth usage. This setup is particularly beneficial in manufacturing environments where real-time data processing is crucial for operational efficiency and rapid response.
Spotlighting an Innovator: Mimik
Mimik, a Canadian technology company, specializes in hybrid edge cloud (HEC) computing. It enables any device to function as a cloud server with applications in automotive, healthcare, and industrial automation.
Mimik recently launched Mimik ai, an operating environment for hybrid edge AI agents. It also joined the NVIDIA Inception program to accelerate AI agent deployment.
At CES 2024, the company collaborated with Marelli to showcase a scalable vehicle architecture solution. Previously, Mimik raised USD 14.3 million in Series A funding to enhance data privacy and reduce costs.
7. Artificial Intelligence
The integration of AI in manufacturing has been rapidly growing, driven by the need for increased efficiency, productivity, and data-driven decision-making.
The global AI in manufacturing market size was valued at USD 5.94 billion in 2024 and is projected to reach USD 230.95 billion by 2034, growing at a CAGR of 44.20%.
Source: Precedence Research
North America is expected to dominate the AI manufacturing market throughout the forecast period. The US AI in manufacturing market size is estimated to be worth around USD 56.17 billion by 2034, growing at a CAGR of 44.55% from 2024 to 2034.
Source: Precedence Research
According to a study, 70% of manufacturers say they have implemented some form of AI into their operations and 82% have plans to increase their AI budgets in 2024.
Leading companies in the AI manufacturing space include Siemens, IBM, Rockwell Automation, GE Vernova, NVIDIA, and C3.AI.
Market Insights & Growth Metrics for Artificial Intelligence
Scale and Magnitude
The artificial intelligence sector includes 107 580+ companies worldwide based on our data. These companies cater to industries and communities in healthcare, financial services, manufacturing, and retail.
On the other hand, Ascendix Tech reports that there are approximately 70 000 AI companies globally as of 2024.
Source: Ascendix
The US leads this sector, hosting about 17 500 AI startups, which accounts for 25% of the global total.
AI ranks 16th in media coverage in our database. This reflects an increasing interest in this technology.
Growth Indicators
AI is gaining traction with a 28.09% annual rise in search interest based on StartUs Insights.
The Asia Pacific region is expected to be the fastest-growing market with a projected CAGR of 19.8% from 2024 to 2034.
Source: Precedence Research
Venture capitalists invested USD 97 billion into AI startups in the US alone in 2024, setting a new record. Global AI private investment reached USD 56 billion across 885 deals in 2024, up 192% from 2023.
Innovation and Novelty
StartUs Insights reports that the AI sector has 84 1390+ patents filed globally. According to WIPO, the number of patent families in AI has grown significantly over the past decade.
From 2014 to 2023, AI patent families increased from 733 to more than 14 000, representing an over 800% increase.
Additionally, AI research has been supported by 23 190+ grants. This surge demonstrates the accelerating pace of AI technological advancements and considers it a critical technology for future success.
The National Science Foundation (NSF) in the US reported funding of over USD 800 million in AI-related activities. This amounted to about 500 new AI projects. While this represents just one country’s contribution, it demonstrates substantial support for AI research.
Top Use Cases of Artificial Intelligence
- Demand Forecasting: AI models process large data and identify patterns and correlations by generating accurate predictions of future demand. Manufacturers analyze seasonal trends, promotional impacts, and even social media sentiment to refine forecasts.
- Supply Chain Optimization: AI algorithms analyze data across various touchpoints in the supply chain to optimize production schedules, transportation routes, and resource allocation.
- Generative Design: AI-driven generative design optimizes component structures by generating multiple design iterations based on material, weight, and performance constraints. Manufacturers use it to create novel designs with increased performance and reduced material waste.
- Process Automation: AI systems monitor production lines in real time to identify bottlenecks and suggest real-time adjustments. For instance, AI optimizes the path of robotic arms to speed up assembly lines.
Noteworthy AI Advancements
- Siemens’ Senseye Predictive Maintenance Solution: The company integrated generative AI to create a conversational and intuitive user interface. This enables manufacturers to take proactive actions more easily, saving time and resources.
- Intel’s Collaboration with Eigen Innovations: Intel implemented Eigen Innovations’ OneView AI platform to inspect production lines and identify defects in real time. This comprehensive inspection approach reduces the cost of quality, which may account for up to 40% of a manufacturer’s revenue.
Core Technologies Connected to Artificial Intelligence
- Neural Networks: Scan products in real time to identify defects with greater accuracy. Neural networks also analyze data from sensors for predictive maintenance and optimize the production processes.
- Transfer Learning: It accelerates model training in the manufacturing sector by leveraging pre-trained models from related domains. Instead of training AI systems from scratch, manufacturers fine-tune existing models on industry-specific data, reducing computational costs and improving accuracy.
- High-Performance Computing: Supports the implementation of asset monitoring and predictive maintenance by enabling the real-time analysis of vast amounts of data to inform decision-making and optimize operations.
Spotlighting an Innovator: Oqton
Oqton, based in the US, specializes in AI-powered manufacturing solutions like additive manufacturing, 3D scanning, and robot welding.
Oqton integrated its Build Quality Suite with EOS machines to enhance print quality. Additionally, Baker Hughes adopted its manufacturing OS, achieving a 98% reduction in monitoring and analysis times.
Backed by USD 40 million in Series A funding, Oqton continues to lead advancements in smart factories and digital transformation technologies.
8. Connectivity Technologies
The global connectivity technology market for manufacturing is projected to grow significantly. This is driven by the adoption of 5G, LoRaWAN, and RFID solutions.
These technologies are expected to enable manufacturers to achieve 30% productivity improvements and up to 20% energy savings.
5G Capabilities in Manufacturing
Source: ABiresearch
5G offers unprecedented capabilities, including 100x faster speeds than 4G, 1 millisecond latency, and support for 1 million devices per square kilometer.
The 5G market is projected to reach USD 11.94 trillion by 2032, with a CAGR of 65.4%, reflecting its transformative potential in enabling advanced communication and IoT integration.
Similarly, the LoRaWAN market is expected to expand rapidly, with forecasts ranging from USD 60 billion to USD 183.9 billion by 2033, driven by its low-power, long-range IoT capabilities.
Source: Dimension Market Research
Meanwhile, the RFID market is set to grow to approximately USD 37.99 billion by 2032, achieving a CAGR of around 11.8%. The RFID tags market alone is anticipated to reach USD 24.55 billion.
Market Insights & Growth Metrics for Connectivity Technologies
Scale and Magnitude
The 5G industry comprises a substantial number of companies globally. According to Mordor Intelligence, the global 5G market is projected to grow from USD 32.74 billion in 2025 to USD 71.17 billion by 2030, reflecting a CAGR of 16.8%.
Despite its transformative potential, 5G ranks 73rd in media coverage among all emerging technologies, indicating that while it is a critical advancement, other technologies may currently be receiving more attention.
LoRaWAN, a key enabler of IoT connectivity, has a smaller footprint with only 1000+ companies specializing in its applications.
The LoRa and LoRaWAN IoT market is expected to grow from USD 10.71 billion in 2025 to USD 44.76 billion by 2030, at a CAGR of 33.1% LoRaWAN also ranks 1543th in media coverage based on our data – reflecting niche but growing interest.
Growth Indicators
Interest in 5G is skyrocketing with a remarkable 114.47% annual rise in search interest based on our analysis.
However, the sector sees a 21.93% decline in five-year funding growth, potentially due to slowed investment cycles after initial large-scale deployments.
Funding for 5G ventures has declined by 21.93%, likely due to slowed investment cycles after initial large-scale deployments.
North America reached 264 million 5G connections by the end of Q3 2024, with 5G accounting for 37% of all wireless connections in the region.
LoRaWAN has also experienced a 68.68% annual rise in search interest. By the end of March 2024, 585 operators in 175 countries and territories were investing in LoRaWAN technology.
However, our data reveals that five-year funding growth has declined by 44.28% – reflecting challenges in scaling adoption beyond niche applications.
Source: Mordor Intelligence
Innovation and Novelty
According to StartUs Insights, 5G witnessed 76 200+ patents filed globally.
Huawei led the 2024 global 5G standard patents ranking with a 12.42% share of patent technology. Qualcomm ranked second with 9.43% of the patent share, followed by LG (8.25%) and Samsung (8.17%).
Research and development in 5G is supported by 1500+ grants. This emphasizes the importance of public and institutional investment in advancing this transformative technology.
LoRaWAN has seen modest but impactful innovation based on our data, with 410+ patents filed globally. The domain also received 80+ grants.
Source: Eureka Select
A review published in 2023 examined 71 patents related to improving LoRaWAN performance, suggesting that the total number of LoRaWAN patents is likely much higher.
Top Use Cases of Connectivity Technologies in Manufacturing
- Worker Safety Monitoring: It ensures real-time monitoring of worker safety through wearable devices and IoT sensors that detect falls, hazardous gas exposure, and extreme environmental conditions.
- Smart Energy Management: Connected sensors and communication protocols allow real-time monitoring of renewable energy systems. This allows grid operators to balance supply and demand effectively.
- Asset Tracking and Management: Leverages RFID tags, GPS trackers, and sensors to monitor the location and condition of equipment, inventory, and materials in real-time. This improves inventory management and supply chain visibility.
- Remote Equipment Diagnostics: Connectivity technologies monitor equipment performance and detect potential faults in real time. This reduces unexpected downtime and minimizes technician visits.
Noteworthy Advancements in Connectivity Technologies
- ZTE, TrueBusiness, and CPF launched a 5G factory: ZTE collaborated with TrueBusiness and CPF to implement a 5G smart factory at CPF’s facility. Utilizing an independent private network called 5G-in-a-box reduces latency while improving coverage and reliability. Leveraging ZTE’s iMacro and UniEngine technologies, it supports advanced applications such as autonomous guided vehicles, robotics, and AI.
- Qualcomm Technologies’ Collaboration with Bosch Rexroth: They worked on industrial automation using 5G time-sensitive networking (TSN). This allows for time-synchronized applications over a live 3.75 GHz 5G private network for precise coordination of industrial processes.
Core Technologies Connected to Connectivity Technologies
- 5G Networks: Connect millions of devices per square kilometer to support advanced applications like real-time automation, predictive maintenance, and seamless IoT integration.
- Single Pair Ethernet (SPE): Uses a single twisted pair of wires to transmit power and data efficiently over long distances. It supports cost-effective and scalable connectivity for sensors, actuators, and other industrial devices.
- Edge Computing: Enables real-time analysis, reduces latency, and ensures faster decision-making critical for time-sensitive manufacturing operations like predictive maintenance and quality control.
Spotlighting an Innovator: Wiliot
Wiliot, an Israeli startup, specializes in IoT solutions, notably its battery-free IoT Pixels and cloud-based Ambient Intelligence Platform, enabling real-time product tracking and data insights.
It recently launched WiliBot, a generative AI chatbot for ambient IoT-connected products. The company partnered with Royal Mail to tag 850 000 containers and initiated a food safety program to support FDA traceability rules.
The company is also backed by a USD 200 million Series C funding round led by led by SoftBank Vision Fund 2.
9. Cybersecurity
The cybersecurity market is projected to reach USD 424 billion by 2030, at a CAGR of 12.63%. This growth is driven by the rapid adoption of connected technologies like IoT and smart grids, which also increase vulnerability.
By 2024, over 65% of AI platforms in the energy industry are expected to include advanced cybersecurity features to safeguard critical systems.
Source: Mordor Intelligence
According to the Critical Start Cyber Threat Intelligence Report, there were 377 ransomware and database leak incidents in the manufacturing and industrial products sector.
Source: Socradar
One of the most notable cyber threat incidents in the manufacturing sector was the ransomware attack on cleaning products maker Clorox, which cost them USD 49 million.
Source: Socradar
The average data breach cost in the industrial sector also increased to USD 5.56 million in 2024, an 18% increase.
Market Insights & Growth Metrics for Cybersecurity
Scale and Magnitude
Our data shows that there are over 172 438 cybersecurity companies worldwide. This large number of companies operating in the cybersecurity sector is reflected in the growing market size, which is projected to reach USD 562.72 billion by 2032, with a CAGR of 14.3%.
Cybersecurity holds the 12th position in media coverage among all emerging technologies based on our data. This reflects its prominence in public discourse and the critical importance of digital security in today’s interconnected world.
Growth Indicators
There has been a 68.27% annual increase in search interest for cybersecurity based on our data. This indicates heightened awareness and concern over digital threats.
Based on our data, funding for cybersecurity ventures has grown by approximately 40.35% over the past five years. In Q1 2024, venture capitalists invested USD 2.7 billion into cybersecurity startups across 154 deals.
Source: Bessemer Venture Partners
Innovation and Novelty
The cybersecurity sector has witnessed substantial innovation, with over 379 402 patents filed globally based on our database. Consequently, this indicates a strong focus on developing advanced security solutions.
In the aerospace, defense, and security industry, Thales filed 18 cybersecurity patents in Q3 2024. The US accounted for 35% of cybersecurity patent filings in the aerospace, defense, and security industries.
Source: Army Technology
Top Use Cases of Cybersecurity in Manufacturing
- Industrial Control Systems Protection: Secures manufacturing operations by safeguarding critical control systems from cyberattacks. It ensures uninterrupted production and prevents operational disruptions.
- IoT Device Security: Protects connected manufacturing devices from unauthorized access and data breaches to maintain system integrity and ensure secure IoT operations.
- Ransomware Prevention: Prevents ransomware attacks by implementing advanced threat detection and response mechanisms. This reduces downtime and protects sensitive manufacturing data.
- Endpoint and Device Security: Shields endpoints like computers, machinery, and mobile devices from cyber threats to secure data exchange and minimize vulnerabilities.
Noteworthy Cybersecurity Advancements
- Claroty’s Cyber-Physical System (CPS) Protection Platform: By providing deep visibility into operational technology (OT and IoT assets, Claroty enables organizations to manage exposure, protect networks, ensure secure access, and detect threats.
- Axonius’ Cybersecurity Asset Management Platform: Delivers a unified view of assets by integrating data from over 800 sources. The platform aggregates normalizes, deduplicates, and correlates device and software information to identify security gaps and automate remediation actions.
Core Technologies Connected to Cybersecurity
- Intrusion Detection and Prevention System (IDPS): Monitors network traffic in real-time to detect and prevent unauthorized access or malicious activities within manufacturing systems. Identifying potential threats early and blocking harmful actions, safeguards sensitive data and ensures uninterrupted production processes.
- Encryption and Cryptographic Protocols: Secure data at rest and in transit by converting it into unreadable formats, accessible only to authorized users. This prevents data breaches, protects intellectual property (IP), and secures communication.
- Multi-Factor Authentication (MFA): Adds an extra layer of security by integrating multiple forms of verification like passwords, biometric scans, or physical tokens.
Spotlighting an Innovator: CloudSEK
CloudSEK, a Singapore-based cybersecurity startup, leverages AI and ML to combat cyber threats. The company’s solutions include XVigil, a digital risk monitoring platform, and BeVigil, a security search engine.
CloudSEK recently reported India as the second most targeted nation for cyberattacks, identified over 31 000 fraudulent customer care numbers, and analyzed 108 ransomware incidents.
The company also uncovered a leak of over 15 000 Fortigate firewall configurations. Backed by USD 10 million in funding, CloudSEK serves top global organizations across banking, healthcare, and retail.
10. Robotic Process Automation
The global robotic process automation market is projected to reach USD 178.55 billion by 2033 with a CAGR of 25.7% from 2025 to 2034.
Source: Precedence Research
The Asia Pacific RPA market is projected to grow at a CAGR of over 46% from 2025 to 2030. This is attributed to several factors such as extensive government support and initiative for digital transformation, wide private sector investments, and a strong presence of RPA solution providers in the region.
Source: Precedence Research
Recently, RPA has been increasingly integrated with AI and machine learning to offer advanced cognitive automation. Gartner predicts that 90% of RPA vendors will offer generative AI-assisted automation to improve customer experience by 2025.
Another report by Gartner also anticipates that more RPA initiatives will move to the cloud in the coming decade, offering greater flexibility and agility to the big corps.
Source: Precedence Research
78% of respondents in an Automation Anywhere survey said they would somewhat or significantly increase automation budgets in the coming 12 months.
Source: Flobotics
Market Insights & Growth Metrics for RPA
Scale and Magnitude
RPA technology has grown significantly with 7700+ companies currently operating in the domain based on our data. Forrester predicts the RPA market will grow to USD 22 billion by 2025, reflecting the demand for advanced automation solutions.
StartUs Insights reports that RPA ranks 760th in media coverage among 20K+ emerging technologies despite its broad applications. This reflects moderate attention compared to others like AI and cybersecurity.
Growth Indicators
Based on our analysis, RPA demonstrates remarkable growth with a 64.02% annual rise in search interest. This reflects increasing adoption across industries.
Over the past five years, RPA has achieved a 255.03% funding growth based on our data.
Source: The Business Research Company
Major companies operating in the RPA and hyper-automation are IBM Corp, Microsoft Corp, SAP SE, and others.
Innovation and Novelty
As per our data, RPA remains a highly innovative domain with 1130+ patents filed globally with RPA-related research supported by 492+ grants.
In 2024, UiPath, a leading RPA company, secured several key patents, including patents for a digital assistant leveraging RPA, implementing RPA in the cloud, as well as executing and resuming RPA workflows, all granted in early 2025.
Top Use Cases of RPA in Manufacturing
- Bill of Materials (BOM) Management: RPA automates the creation and updates of BOM in automotive and electronics manufacturing. It ensures accuracy and reduces errors.
- Invoice and Payment Processing: RPA streamlines invoice generation, validation, and payment tracking in supplier-intensive industries like machinery and aerospace.
- Production Planning and Scheduling: RPA integrates real-time data for production planning in high-volume sectors such as consumer goods and pharmaceuticals. It optimizes resource allocation, minimizes downtime, and enhances operational efficiency.
- Compliance and Audit Management: It automates compliance checks and audit reporting in regulated industries like food and beverage and healthcare manufacturing. This ensures adherence to standards, reduces risks, and saves time.
Noteworthy RPA Advancements
- UiPath’s Integration of AI: The company’s AI Center enables software robots to perform cognitive tasks such as understanding text, making decisions, and predicting outcomes. This integration extends automation capabilities to complex and decision-based processes.
- Pega Systems’ Low-Code Automation Platform: Allows users to design sophisticated, automated workflows without extensive coding. This model-driven development approach allows developers to accelerate application development and foster collaboration.
Core Technologies Connected to RPA
- Optical Character Recognition (OCR): Automates the extraction of text and data from scanned documents, images, and PDFs. Using this, manufacturers digitize paper-based processes like invoicing, quality checklists, and inventory logs.
- Integration Platforms: Connect disparate systems, tools, and software within manufacturing operations for seamless communication and data sharing across ERP, CRM, and IoT systems. This streamlines workflows ensures consistency and enables end-to-end automation.
- Natural Language Processing: Enables RPA systems to understand and process human language in tasks such as analyzing maintenance logs, interpreting customer queries, or generating reports.
Spotlighting an Innovator: LAIYE
Laiye, a China-based intelligent automation company, provides AI-powered solutions like RPA, intelligent document processing, and conversational AI for industries like logistics, retail, healthcare, and more.
Laiye recently launched AI Agent products to boost productivity, earned recognition in Gartner’s RPA report for the fourth consecutive year, and was named a “2024 Go-International Brands TOP 30” by Forbes.
Backed by USD 160 million in Series C funding, Laiye has expanded globally, serving over 300 Fortune 500 companies.
Key Benefits of Digitizing Manufacturing Businesses in 2025
Source: Whatfix
1. Enhanced Quality
Digital transformation enables real-time monitoring and AI-driven quality control to reduce defects and improve product consistency.
For example, GE Aviation uses AI and digital twins to analyze jet engine data during production and enhance overall product quality.
2. Increased Process Efficiency
By integrating IoT, robotics, and automation, manufacturers streamline processes and reduce downtime.
For instance, Siemens implemented smart factory technologies in its Amberg facility, minimizing errors while increasing output efficiency.
3. Increased Profit Margins
Automation and predictive analytics lower operational costs and optimize resource usage.
Procter & Gamble leveraged digital tools to collect equipment data and create new products or customize product lines.
4. Supply Chain Optimization
Digital tools provide real-time supply chain visibility, enabling better inventory management and demand forecasting.
Caterpillar implemented machine learning systems for predictive analytics to reduce maintenance costs and ensure timely project completion.
5. Improved Customer Experience
Digital transformation allows personalized production and faster delivery times.
Nike uses digital platforms to offer customizable products, such as shoes tailored to individual customer preferences, to improve customer satisfaction and brand loyalty.
6. Sustainability
Digital solutions optimize energy use, minimize waste, and support eco-friendly manufacturing practices.
Unilever adopted IoT and AI technologies in its factories to cut water and energy usage while reducing costs.
Step-by-Step Guide: Digital Transformation Strategy for the Manufacturing Sector
Developing a comprehensive digital transformation strategy is crucial for manufacturing companies seeking to improve operational efficiency, integrate smart technologies, and stay competitive in an evolving industrial landscape. The following step-by-step guide outlines a structured roadmap, incorporating insights from industry leaders and best practices to drive successful digital adoption in manufacturing.
1. Define the Vision and Goals
Establish a Clear Vision: Align the digital transformation strategy with the company’s mission, focusing on objectives like enhancing production efficiency, sustainability, and supply chain resilience.
Set Measurable Objectives: Develop specific, quantifiable goals—such as reducing production downtime, optimizing energy consumption, increasing automation levels, or improving product quality metrics.
2. Conduct a Digital Maturity Assessment
Evaluate Current Capabilities: Assess existing digital tools, manufacturing processes, and workforce skills to identify gaps and opportunities for improvement.
Benchmark Against Industry Leaders: Compare your organization’s digital maturity with top manufacturing companies to understand competitive positioning and identify best practices.
3. Identify Key Technologies
Prioritize Investments: Focus on high-impact technologies, such as Industrial IoT (IIoT) for real-time equipment monitoring, AI for predictive maintenance, and robotics for process automation.
Ensure Scalability: Select solutions that can adapt to future technological advancements and support business expansion.
Use Technology Scouting: Leverage platforms like StartUs Insights Discovery Platform to track emerging manufacturing innovations and trends.
4. Build a Robust Data Infrastructure
Leverage Big Data: Implement systems to collect, store, and analyze real-time manufacturing data from IoT-enabled machinery, production lines, and quality control systems.
Integrate Systems: Ensure seamless connectivity between operational technology (OT) and information technology (IT) systems to optimize production workflows and enhance decision-making.
5. Develop a Detailed Roadmap
Plan Incremental Implementation: Break down the transformation journey into manageable phases—starting with pilot projects to test and refine digital initiatives before full-scale deployment.
Set Realistic Timelines: Establish achievable deadlines for each phase while allowing flexibility to adapt to unforeseen challenges.
6. Foster Collaboration and Ecosystem Partnerships
Engage Stakeholders: Involve employees, suppliers, customers, and technology partners early in the process to ensure alignment and adoption.
Form Strategic Alliances: Partner with technology providers, startups, and research institutions to integrate cutting-edge manufacturing solutions and share industry knowledge.
7. Upskill the Workforce
Invest in Training: Provide training programs to develop employees’ digital competencies, ensuring they can effectively operate new automation and analytics tools.
Cultivate a Digital Culture: Encourage continuous learning and innovation to drive adoption and optimize technology utilization across the workforce.
8. Implement Robust Cybersecurity Measures
Protect Critical Assets: Deploy comprehensive cybersecurity frameworks to safeguard industrial control systems, proprietary manufacturing processes, and supply chain data.
Comply with Regulations: Adhere to industry standards and legal requirements related to data security, operational safety, and intellectual property protection.
9. Monitor, Measure, and Optimize
Track Key Performance Indicators (KPIs): Regularly assess progress against established metrics, such as production efficiency, machine downtime reduction, and energy savings.
Adapt Strategies: Utilize data-driven insights to refine digital transformation efforts—addressing new challenges and capitalizing on emerging opportunities.
10. Scale and Innovate Continuously
Expand Successful Pilots: Scale up proven digital solutions across multiple production lines and facilities to drive enterprise-wide transformation.
Embrace Continuous Improvement: Stay ahead of technological advancements and industry shifts, fostering a culture of ongoing innovation and process optimization.
Future Trends in the Manufacturing Industry: Top 4 Emerging Technologies
1. Decentralized Manufacturing
What’s next: Manufacturing will shift towards localized production using 3D printing, IoT-enabled monitoring, and cloud computing for distributed data management.
Why it matters: Reduces transportation costs, enhances supply chain resilience, and enables on-demand production closer to end consumers.
2. Metaverse Monitoring
What’s next: Immersive technologies like AR, VR, and digital twins will enable real-time visualization and remote management of production processes.
Why it matters: Allows for better collaboration across teams, predictive maintenance, and faster response to operational challenges.
3. Experience Hubs
What’s next: Mixed reality (MR), AI, and haptic feedback will power immersive product demonstrations and personalized customer interactions.
Why it matters: These hubs transform customer engagement, enhance co-creation, and support the adoption of new technologies through hands-on experiences.
4. Advanced Workforce Training
What’s next: AR/VR environments and AI-powered personalized learning systems will offer immersive training and continuous upskilling opportunities.
Why it matters: Addresses the skills gap in manufacturing, facilitates knowledge transfer, and prepares the workforce for the adoption of advanced technologies.
Act Now to Stay Ahead of the Technology Curve
Staying competitive means more than just being aware of technological advancements. Every industry faces unique challenges and opportunities, and a one-size-fits-all approach isn’t enough.
That’s where our AI and Big Data-powered Discovery Platform comes in. With access to over 4.7 million emerging companies and 20K+ technologies & trends globally, it equips you with the actionable insights you need to stay ahead of the curve. Leverage this powerful tool to spot the next big thing before it goes mainstream. Stay relevant, resilient, and ready for what’s next.
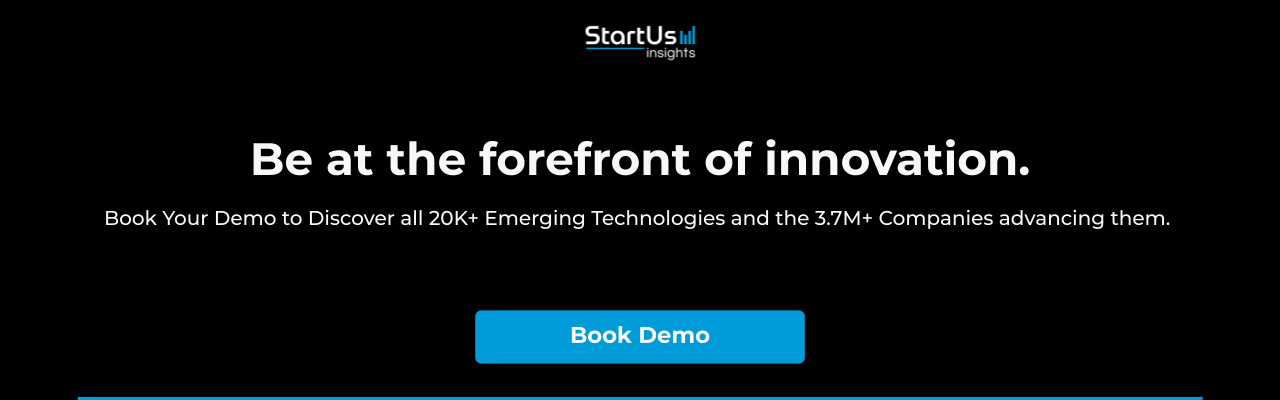