This data-driven research explores the top 10 steel industry trends that pave the way for modern steelmaking. The steel industry is seeing advancements in technologies that change the way steel is produced. Smart steel technologies like augmented reality (AR) and virtual reality (VR) offer an immersive training environment and allow the workforce to interact with real-world assets and tools. 3D printing, smart manufacturing, and robotic automation improve the performance and efficiency of steelmaking processes.
What are the Top Steel Industry Trends (2025)?
- Advanced Coating
- Smart Steel Manufacturing
- Recycled Steel
- 3D Printing
- Robotic Automation
- Laser-Aided Forming
- Hydrogen-Fueled Steel Production
- Carbon Capture
- Predictive Maintenance
- AR & VR in the Steel Industry
Methodology: How We Created the Steel Industry Trend Report
For our trend reports, we leverage our proprietary StartUs Insights Discovery Platform, covering 5M+ global startups, 20K technologies & trends plus 150M+ patents, news articles, and market reports.
Creating a report involves approximately 40 hours of analysis. We evaluate our own startup data and complement these insights with external research, including industry reports, news articles, and market analyses. This process enables us to identify the most impactful and innovative trends in the steel industry.
For each trend, we select two exemplary startups that meet the following criteria:
- Relevance: Their product, technology, or solution aligns with the trend.
- Founding Year: Established between 2020 and 2025.
- Company Size: A maximum of 200 employees.
- Location: Specific geographic considerations.
This approach ensures our reports provide reliable, actionable insights into the steel innovation ecosystem while highlighting startups driving technological advancements in the industry.
Innovation Map outlines the Top 10 Technology Trends in the Steel Industry & 20 Promising Startups
For this in-depth research on the Top Steel Manufacturing Trends & Startups, we analyzed a sample of 650+ global startups & scaleups. The Steel Manufacturing Innovation Map created from this data-driven research helps you improve strategic decision-making by giving you a comprehensive overview of the steel industry trends & startups that impact your company.
Tree Map reveals the Impact of the Top 10 Steel Industry Trends
Based on the steelmaking Innovation Map, the TreeMap below illustrates the impact of the Top 10 Technology Trends in the Steel Industry. Startups and scaleups use smart manufacturing, robotic automation, and green steel technology to speed up production.
Immersive technologies enhance safety training and offer visual aids on the shop floor. Advanced nanocoatings, carbon capture solutions, and hydrogen-based processes cut emissions and produce clean steel. Other trends include laser forming for part precision and predictive maintenance for extending asset life.
Global Startup Heat Map covers 670 Steel Manufacturing Startups & Scaleups
The Global Startup Heat Map showcases the distribution of 650+ exemplary startups and scaleups analyzed using the StartUs Insights Discovery Platform. It highlights high startup activity in Europe and the US, followed by India. From these, 20 promising startups are featured below, selected based on factors like founding year, location, and funding.
Want to Explore Steel Industry Innovations & Trends?
Top 10 Recent Trends in the Steel Industry (2025)
1. Advanced Coating
Advanced coating plays an important role in the steelmaking industry by enhancing surface performance, durability, and quality of steel products. Galvanizing and polymer coatings provide resistance to corrosion and abrasion by applying thin layers of polymers like epoxy and polyester.
Also, coatings like ceramic as well as thermal sprays and passivation contribute to the overall longevity and aesthetic appeal of steel products. This enables a variety of applications in the construction, aerospace, automotive, and manufacturing industries.
Further, the coated steel market was valued at over USD 57.5 billion in 2023. It is estimated to register a CAGR of over 1.7% between 2024 and 2032.
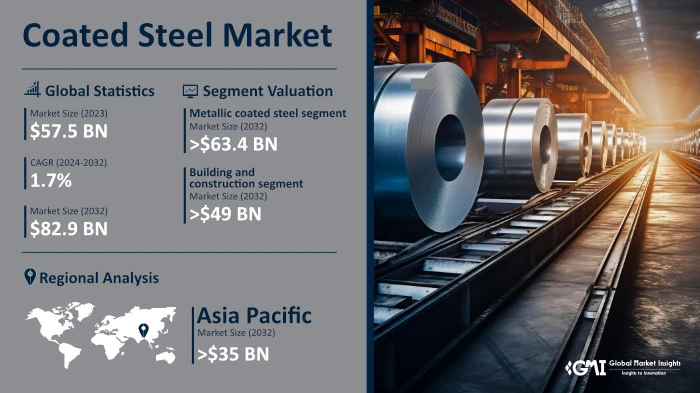
Credit: Global Market Insights
Allium Engineering offers Coated Rebar Technology
US-based startup Allium Engineering provides coated rebar technology for the steel industry. It increases the steel products’ lifetime and reduces carbon emissions. For this, the startup uses a thin stainless steel layer and a protective oxide barrier coating to shield the steel core against corrosion.
The coating prevents rust and water buildup on the surface of the steel rebar to ensure better performance. Allium Engineering allows the construction industry to coat steel and concrete structures exposed to the environment to reduce emissions and maintenance costs.
Thintech Coatings protects Metal Surfaces
Vietnamese startup Thintech Coatings develops Metal Coating, a solution that enhances durability, corrosion resistance, and performance across industries. Its proprietary coating technology forms a protective layer that bonds at the molecular level to create a barrier against wear, oxidation, and environmental damage. The coatings use nanomaterials to improve surface hardness, reduce friction, and extend the lifespan of metal components.
The startup’s Metal Coating protects metal surfaces such as iron, steel, stainless steel, aluminum, galvanized steel, copper, bronze, powder-coated metals, and painted and primed metals. Thintech Coatings offers a cost-effective alternative to traditional coatings while maintaining thermal and chemical stability. It delivers innovative surface protection that increases efficiency, reduces maintenance costs, and enhances the reliability of metal structures and machinery.
2. Smart Steel Manufacturing
Smart manufacturing processes incorporate industry 4.0 solutions and the Industrial Internet of Things (IIoT) to transform steelmaking. Advanced steel technologies and data-driven solutions optimize production processes, increase efficiency, and enhance product quality.
For example, data analytics, machine learning, advanced sensors, and monitoring systems enable early detection of issues and provide precise control of machinery. The technologies also help in the supply chain optimization of raw steel by integrating data from suppliers, inventory systems, and production schedules.
Foresight Data Machines develops Process Control Solutions
Foresight Data Machines is a UK-based startup that builds process control solutions for EAF steelmaking. Its AI-enabled solution understands the relationship between raw material quality and operating procedures to provide meaningful insights.
The solution translates the data into actionable process control recommendations to improve energy and raw material efficiency, yield, and quality. Foresight Data Machines thus helps operators, process engineers, plant managers, and purchasing teams in raw material inventory and quality management.
XYMA Analytics creates Measurement Sensors
Indian startup XYMA Analytics provides multi-point sensing, temperature, and level management sensors for steel manufacturing businesses. It offers μTMaps and μSTMaps – two multi-point high-temperature mapping sensors that use a single waveguide sensor technology.
The sensors feature insulation damage and humidity control to detect abnormal temperature drops and possible humidity and insulation damage in the pipelines. XYMA Analytics empowers steel manufacturers by safeguarding their processes and enhancing productivity.
3. Recycled Steel
One of the recent trends in the steel industry is the use of recycled scrap materials as the primary raw material. The recycling of metals takes place in an electric arc furnace, which provides an energy-efficient alternative to traditional steelmaking.
The process involves collecting and sorting scrap metal, including end-of-life steel products, to melt and refine the alloys and adjust composition in an EAF.
Recycled steelmaking offers many environmental benefits such as lowering carbon emissions and reducing the wastage of valuable natural resources. This allows manufacturers to reduce costs of production and achieve net zero emissions.
Moreover, the sustainable (recycled and green) steel market size was valued at USD 335.4 billion in 2023. It is predicted to reach USD 604.3 billion by 2031, with a CAGR of 7.8% from 2024 to 2031.
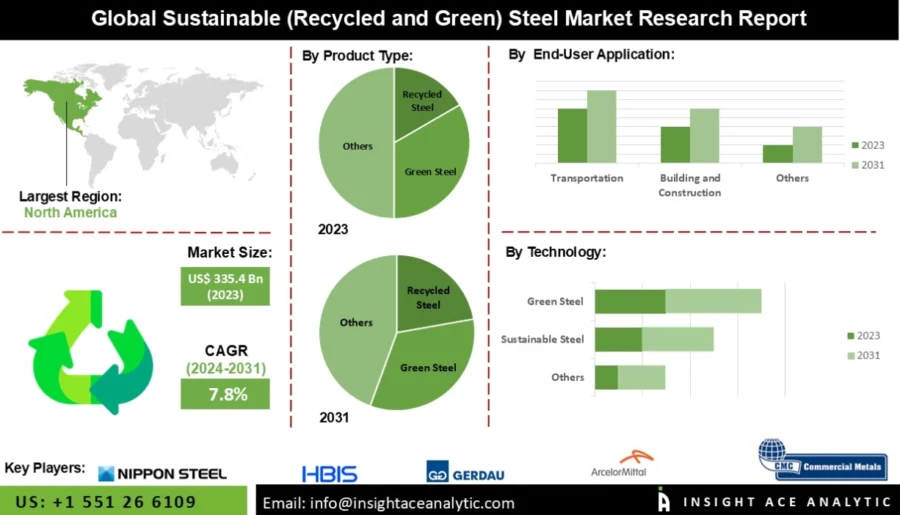
Credit: InsightAce Analytic
PRINZ Blades advances Low-Carbon Steelmaking
German startup PRINZ Blades manufactures green steel from EAF and renewable energy. The startup uses recycled steel scraps and alloys, along with a photovoltaic system with multiple solar modules, to manufacture a range of blades. The blades tamper with a hardening process for an optimal balance of tenacity and hardness to offer increased durability and performance.
With resource-efficient and environmentally friendly processes and raw materials, the startup allows steel manufacturers to increase process sustainability. PRINZ Blades offers product lifetime optimization, welding, and maintenance solutions to direct customers and industries.
POSCORE streamlines Steel Scrap Recycling
POSCO is a South Korean startup that specializes in transforming steel scraps into valuable products. The company focuses on recycling electrical steel scrap, a material typically challenging to process in traditional steelmaking. POSCO’s innovative process extracts high-purity magnetic powder from this scrap, a critical component for electric vehicle motors.
By diverting steel scrap from landfills and transforming it into a high-demand product, POSCO contributes to a circular economy while addressing the growing need for sustainable materials in the automotive industry.
4. 3D Printing
3D printing is one of the most reliable processes to manufacture complex metal parts, components, and prototypes. Traditional steelmaking works on subtractive principles like cutting, shaping, milling, and grinding, which increases the scraps from production.
Additive manufacturing enables the direct fabrication of steel parts layer by layer to eliminate wastage. It uses powder bed fusion and direct energy deposition technology to melt the metal powder.
For melting, a 3D printer utilizes a laser, electron beam, or plasma arc to make parts for precise applications. Such advanced steel technology allows steel product manufacturers to make parts with precision and eliminate raw material wastage.
The global 3D printing metal market size was valued at USD 1.0 billion in 2024. It is expected to grow at a CAGR of 17.3% from 2025 to 2030. The stainless steel segment is projected to be the fastest-growing, with a CAGR of 15.8% over the forecast period.
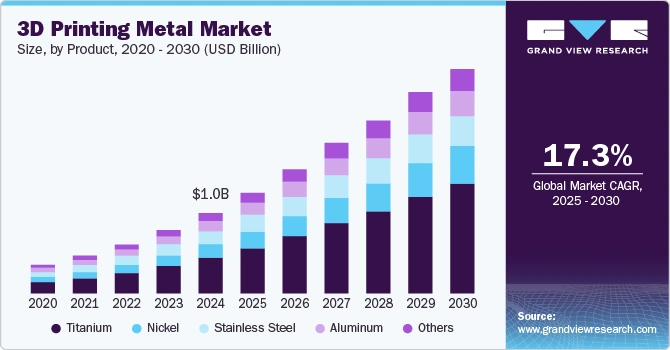
Credit: Grand View Research
Aditiv Solutions deploys Metal Additive Manufacturing Solutions
Aditiv Solutions is a startup from South Africa that designs and builds metal additive manufacturing equipment. Its HYRAX is a 3D printing system that allows the development of intricate parts directly from metal powder.
The solution uses powder bed fusion technology equipped with precision lasers and optical systems to ensure quality. Aditiv Solutions deploys machine design, simulation, code development, and product life-cycle management to offer cost-effective manufacturing solutions to steel manufacturers.
Headmade Materials provides Additive Material for Powder Metallurgy
German startup Headmade Materials offers materials for the 3D printing and powder metallurgy industries. Its sinter-based ColdMetalFusion technology provides high-strength eco-friendly parts to simplify cleaning and handling.
The startup’s feedstock fits into existing machines and processes to eliminate new equipment costs and help in producing quality metal parts. Headmade Materials embeds metal powders in a plastic matrix that allows better metal particle binding to improve occupational safety in additive manufacturing and automotive industries.
5. Robotic Automation
Robotic automation plays a vital role in modern manufacturing processes. It revolutionizes the steel industry by improving efficiency, productivity, safety, and quality control. By incorporating technologies like AI and continuous monitoring, steel manufacturers automate their plants with greater efficiency.
Robots in steelmaking enable autonomous raw material handling, assisted welding and assembly, continuous casting, and automated furnace operations. Robotic automation also allows manufacturing plant owners and managers to streamline repetitive and dangerous tasks by removing the need for direct human involvement.
Wattman delivers AI-Powered Robotic Manufacturing
Chinese startup Wattman provides industrial intelligence with robots, machine vision, and 3D intelligence perception to steel manufacturers. It offers WATT iRobot, a smart robot series for anode carbon block cleaning and target object repairing.
The startup’s robots feature camera-based arms for performing 3D reconstruction and analysis of objects. It also offers intelligent mucking and palletizing robots to enable the automatic handling of stacking operations for steel. This way, Wattman develops a smart lifecycle management system for metallurgical furnaces, improving the operational efficiency of steel plants.
Mech-Mind Robotics enables Intelligent Robot Control
German startup Mech-Mind Robotics offers solutions for intelligent robot control using 3D simulations. The startup offers Mech-Viz, a robot programming software for path planning, collision detection, and grasp planning.
The all-in-one system enables the programming of robots visually and code-free by using AI to calculate the fastest motion sequence. By integrating a robot controller with Mech-Viz, Mech-Mind helps automotive, logistics, home appliance, and steelmaking industries utilize autonomous robots for process automation.
6. Laser-Aided Forming
Modern steelmaking utilizes new technologies in terms of manufacturing, bending, and forming. Laser-aided forming uses high-power laser beams for metal deformation, forming, and precision control. It offers unique capabilities for shaping and forming metal components with high precision over traditional technologies.
Laser forming also reduces tooling requirements, improves formability, and allows for complex shape geometries. This technology reduces spring back in formed parts by inducing compressive stresses during the forming process. Further, laser beams enable steel manufacturers to achieve bends, complex contours, and sharp angles with higher accuracy in complex productions.
Applied Impulse advances Impulse Manufacturing for Steelmaking
US-based startup Applied Impulse uses electrical and optical pulsed power for impulse manufacturing in steel factories. It uses laser ablation technology with parasitic ionization to weld thick aluminum sheets to steel parts to improve corrosion resistance.
The solution utilizes a vaporizing conductor and electromagnetic induction to pass a high transient current between the sheet and the workpiece. Applied Impulse’s technology offers welding, cutting, shaping, conformal interference joints, and ballistic additive manufacturing to part manufacturers and steel-forming industries.
SG Metals aids Plasma and Laser Melting
SG Metals is a US-based startup that provides thick steel plates, steel shearing, bending, and sawing solutions. It uses an in-house steel precision laser and high-definition plasma cutting technologies for commercial, manufacturing, and industrial applications.
With automatic feeds and measuring devices for precision accuracy, the technology enables the manufacturing of structural and coil steel. SG Metals caters to automobile factories, construction sites, and manufacturing plants.
7. Hydrogen-Fueled Steel Production
Traditional steel production relies heavily on fossil fuels, such as coal and natural gas, which emit carbon dioxide (CO2) and contribute to greenhouse gas emissions and climate change. Startups now use hydrogen as a reducing agent in the direct reduction of iron ore to form sponge iron.
Further, hydrogen acts as a clean source of heat in EAFs that enables steelmakers to produce green steel. For generating hydrogen, companies use methods like steam methane reforming (SMR), electrolysis, methane pyrolysis, and biomass gasification. This ensures a sustainable and cost-effective supply of hydrogen in steelmaking plants.
Hystar develops Proton Exchange Membrane Electrolysers
Hystar is a Norwegian startup that develops proton exchange membrane (PEM) electrolyzers for green hydrogen production from water electrolysis. It offers Vega, Mira, and Orion, modular and scalable electrolyzer systems that utilize its patented technology.
The solution features full containerized systems for rapid deployment of autonomous and independent electrolyzers without any additional constructions. It uses thin membranes, anode air feed, and cathode water feed for efficient operations and higher output. This enables Hystar to deploy green steel solutions to reduce carbon emissions and optimize the cost of the steel manufacturing plant and processes.
ELECTRIC HYDROGEN provides an Integrated Electrolysis Technology
US-based startup ELECTRIC HYDROGEN creates electrolyzer technologies for clean, abundant, and low-cost hydrogen. It leverages renewable energy sources to generate sustainable hydrogen for heavy industries.
The startup designs and provides integrated electrolysis plants to improve performance and reduce capital and operating expenditures. Additionally, ELECTRIC HYDROGEN allows plant managers to predict operations and production to reduce project costs and prevent schedule overruns.
8. Carbon Capture
Carbon capture technology enables CO2 emissions capture during steel production. This technology uses pre- or post-combustion capture to collect carbon. The captured CO2 is stored underground for enhanced oil recovery (EOR) or the production of chemicals, polymers, and construction materials.
Integrating carbon capture into the steelmaking industry enables plant owners to achieve net-zero emissions, promote DRI-based steelmaking, and fight climate change.
Verde CO2 develops Carbon Capture & Storage (CCS) Solutions
US-based startup Verde CO2 makes carbon capture and storage solutions for carbon reduction in the steelmaking industry. It manufactures CO2 capture equipment to improve carbon capture and storage for a net-zero environment.
The startup offers geologic analysis to identify viable sequestration reservoirs for CO2 separation from fossil or biomass-fuelled power plants and industrial facilities. This enables Verde CO2 to transport, store, and use collected carbon as input and feedstock for steel production facilities and industries.
Capture6 enables Irreversible Carbon Capture
US-based startup Capture6 provides permanent and irreversible carbon capture solutions for reducing GHG emissions in the environment. Its solution uses a direct air capture (DAC) approach for carbon removal to increase freshwater supply for agricultural uses.
The startup features point source capture for ethanol, fertilizers, steel, and cement manufacturing industries to create longer decarbonization timelines. Capture6 effectively captures and stores carbon for higher geological timescales with its mineralizing process.
9. Predictive Maintenance
By leveraging real-time data and machine learning algorithms, steel manufacturers predict potential failures and schedule maintenance activities proactively. Temperature, vibration, and energy consumption data help systems to monitor deviations and provide actionable insights to plant managers.
Real-time monitoring of equipment also detects early signs of deterioration or abnormalities. By continuously analyzing data from sensors, maintenance teams take timely action by identifying deviations from normal operating conditions.
Deep Meta facilitates Metallurgical Defect Prediction
Deep Meta is a UK-based startup that provides a digital twin platform to analyze and predict metallurgical defects in production plants. The startup’s software harnesses historical data to create digital versions of potential defects to optimize production output.
It offers real-time insights for warning operators about casting cracks and rolling defects to reduce the wastage and costs of raw materials. Deep Meta tracks and monitors the steel remotely in the supply chain and predicts material behavior and lifecycles for better allocation of resources in modern steel plants.
Bayanatai offers a Defect Detection Algorithm
Bayanatai is a startup from Qatar that develops defect detection algorithms to identify surface defects on steel sheets. It implements AI algorithms to predict the location and type of imperfections in steel manufacturing.
The solution leverages machine learning to provide real-time analysis, intelligent solutions, and prediction models to make better strategic decisions in steelmaking plants. Bayanatai caters to the construction, retail, and industrial sector by providing object detection, prediction models, and natural language processing (NLP) solutions. This allows industries to make deliver better customer experiences.
10. Immersive Technologies
AR provides a realistic and interactive training environment for steelworkers. Immersive simulations replicate complex steelmaking processes. They allow employees to practice operating machinery, handling equipment, and performing maintenance tasks in a safe and controlled virtual environment.
Additionally, it enables manufacturers to visualize steel products, plant layouts, and equipment designs for engineers to create virtual models and identify potential issues before physical construction.
Eterio Realities enables AR-assisted Steel Production
Canadian startup Eterio Realities creates integrated AR production software tools for first-line workers to improve production cycles. It offers FabStation-Steel, an AR solution that visually places 3D assets into workflows for construction and inspection workers.
Its AR-based steel production tools for fabrication floors allow for real-time reporting and data exchange. By doing so, Eterio Realities provides status updates as well as time and material tracking to improve production performance in steel plants.
Warp VR provides VR-enabled Workforce Training
Warp VR is a Dutch startup that creates VR workforce training solutions to upskill the workforce and improve performance. It utilizes a story-based immersive learning approach to train the workforce and improve completion rates and retention.
The solution works on multiple devices and supports learning management system (LMS) integrations, single sign-on (SSO), and multiple languages. This way, Warp VR empowers instructor-led, on-the-job, and online training remotely, fostering employee skill development and bolstering their confidence.
Discover all Steel Industry Trends, Technologies & Startups
The future of steelmaking is set for significant transformation with the integration of advanced technologies like AR/VR and advanced coatings. By using cyber-physical systems (CPS), AI, and IoT, the steel industry embraces digitalization to create smart and connected plants. The industry also seeks to adopt cleaner energy sources like hydrogen, renewable electricity, and advanced carbon capture solutions to reduce GHG emissions.
The steel manufacturing trends & startups outlined in this report only scratch the surface of trends that we identified during our data-driven innovation & startup scouting process. Identifying new opportunities & emerging technologies to implement into your business goes a long way in gaining a competitive advantage.